Garment Manufacturing Process From Raw To Finished Product
The garment manufacturing process includes all the cloth-making processes from sketch to the finished product, including cutting, sewing, and finishing.
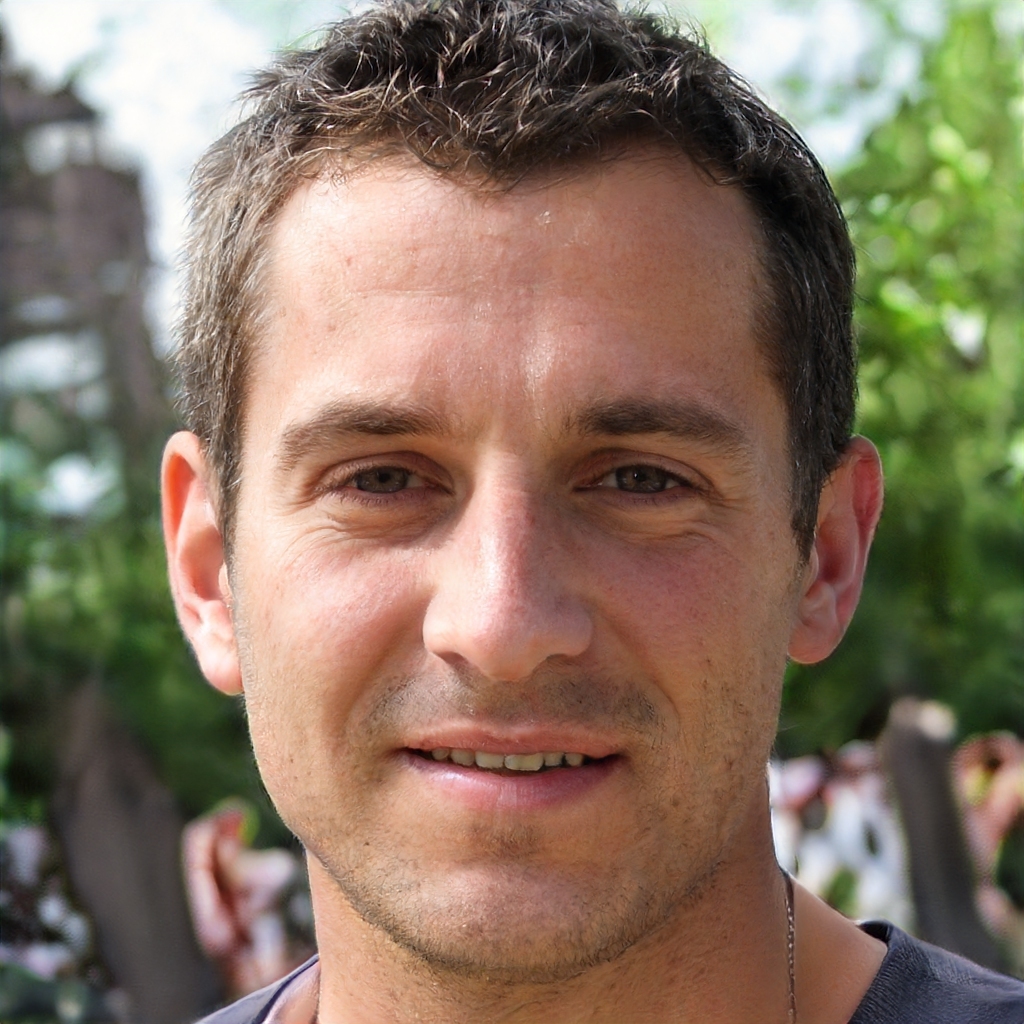
The manufacturing of clothes is a vast distributed process in which all operations are performed in different sectors/departments. Garment manufacturing is a sequential series of methods and procedures such as designing, laying, marking, cutting, sewing, finishing, pressing, packaging, sampling, etc. This is how the garments are turned into finished products from Raw materials.
Start To End Process of Manufacturing Clothes
The clothing manufacturing process includes different methods such as costs, quality checks, evaluation of sizing and fitting, costs, and a lot more strategies to produce a diverse range of product mixes. Here is a whole start to end process of manufacturing clothes.
-
Design & Development
The design and development is the initial stage from which product manufacturing starts. In this process, the styling and designing of cloth are set up. In this phase, the primary goal is to create the product's design according to your requirements, making it functional. The initial steps for exploring design ideas are researching, attending trade shows, following trends, following fashion icons, fashion magazines, etc.
The customer makes anything popular so that you can start with anything trendy in the market. Pick the product and start sketching your designs. After making the design, you need to select the fabric for the cloth making. You'll have to choose the product according to the customer's requirements.
-
Dyeing of Clothes
Custom dyeing comes in place when the customer is looking for personalized clothing. In this situation, the dyeing of fabrics is the best option by which the manufacturer can obtain any type of design they are looking for. Fabric dyeing is a popular method by which you can give a new look to fabric by dyeing it into a bright, vibrant, and new hue of color.
There are endless customization options with fabric dyeing like Tie Dye, sulphate dye, Dip Dye, Neon Dye, direct color Dye, Reactive Color Dye, color sprinkling, etc.
Different chemicals are used in the cleaning of fabrics. There are different types of fabric finishing
- Improves the appearance of fabrics.
- Improves the performance and durability of fabrics.
- Leaves clothes with special features.
-
Pattern Making
After the design is developed, the pattern is created for the t-shirt, hoodies, shorts, or any product. To do this, you need to sketch out the design over the paper and then cut & sew the individual pieces of the garments.
The pattern of clothes helps in creating the shape of the garment. After the pattern is created for the fabric, the product construction process starts. There are different methods to create patterns, but the widely used method is paper cardboard.
The cardboard is used to create the outline of the garment. After the tracing, the fabric is cut. Moreover, CAD (Computer-Aided Design) is another method for making clothing patterns.
The patterns are an important and helpful part of the process as it helps ensure the correct sizing, fitting, and measurements of the cloth.
-
Grading of Fabric
After the pattern creation, the fabric is graded to ensure the product will fit various sizes. The material is graded based on the different patterns for making different sizes. After the cutting process, the garment is undergone a number of a process called "grading." Grading refers to making different sizes of clothes from the patterns developed.
The grading is done by making minor changes to the pattering pieces. Grading is of two types vertical and horizontal. The horizontal grading refers to the modification in widths from the base, while the vertical grading refers to the change in the length of the pattern.
Grading of the fabric pattern allows for creating and manufacturing a vast range of clothes sizes from a limited piece.
-
The Cutting Process
The fabric is marked and cut down into different components in this step. The marking process indicates to the operators where to cut, and this is how cutting is done using the markings and line. There is a number of ways by which you can mark the fabric. After the fabric marking, the cutting process starts.
Now, different machines are used for cutting. Commonly used machines are a rotary cutter, scissors, or a knife. Be sure to use the sharp tools when cutting the fabric, or else you'll face tearing and fraying of the material.
Marking and cutting are essential elements of garment manufacturing. Most cut and sew manufacturers do this. Marking over fabric for cutting help in creating up to requirements and finished product.
-
The Sewing Process
Here the sewing process starts, where the individual components of the clothing are sewed together manually by hands or by using machines. Different products are joined together in this process, making up a garment.
Manual by hand sewing is comparatively slow and takes more effort, but it produces high-quality intricate stitching. Machine sewing can be faster, but less precise. Different stitches will be done depending on what kind of fabric is being sewn onto. Here are some of the stitches types:
- Button Holes
- Zigzag Stitches
- Straight stitches
-
The Finishing Process
Here comes the final process of garment manufacturing. This part includes pressing and adding any minor details changes that the customer requires to make it a complete finished product.
Manual by hand sewing is comparatively slow and takes more effort, but it produces high-quality intricate stitching. On the other side, the machine can sew faster, but it's less precise than hand sewing. Different types of stitching are done based on the kind of fabric on which you are sewing. Here are some of the stitches types:
- Buttons
- Zippers
- Snaps
- Appliques
It includes all the methods that can help improve the functionality and appearance of the clothes. The clothes finishing are performed over both types of clothes, woven or knitted. The standard finishing process includes bleaching, custom fabric dyeing, printing, washing, and coating.
The Workflow of the Garment Manufacturing Process
Here is the workflow of the garment manufacturing process, from start to end and all the process changes that are involved in the garment manufacturing process.
Fabric development → Fabric Lab dip preparation → Fabric approval → Pattern making → Garment sampling → Sample approval (Prototype, fit, size set, salesman's sample) → Final pattern making → Pattern grading → Fabric purchasing → Fabric inspection → Fabric shade banding → Segregation of fabrics by its widths and shade band → Fabric testing → Issue fabric for cutting section → Fabric layering → Marker making → Cutting the lay → Sorting of cut components → Layer numbering → Cut bundling and tagging → Issue to stitching floor → Stitching process → Quality checking of garment inline and end-of-the line → Garment repair → Garment washing → Garment finishing → Finished product folding & Packing → Shipment inspection → Approved garments are ready ship.
This chart mentions all the process that are involved in the manufacturing process of the garment and mentions all process so that you can understand the whole process easily. Moreover, there are pre-production stages involved in the manufacturing process. Here are these listed:
There are different types of Garment manufacturing processes used in manufacturing factories. Here is a quick look at all kinds of the manufacturing process:
- Garment sampling
- Trims approval
- Pattern making
- Trim sourcing
- Fabric sourcing
- PP Meeting
Different Types of Garment Manufacturing Process
-
Section Production System
There are different types of Garment manufacturing processes used in manufacturing factories. Here is a quick look at all kinds of the manufacturing process:
In this clothing manufacturing system, the operations are divided into different sections. All the machines that perform similar functionality are grouped to perform the operations over a product.
For Example: For the making of the T-shirt, all the machines of similar functionality are placed together and operate in one department, such as making collars, sleeves, and cuffs are developed in one department and then move on to the following department of the assembly section.
-
Make Through System
The tailor works alone over the garment in the make-through-make system. The tailor is the only one who works over pattern making, cutting the fabric, sewing, and finishing the garment till packaging. In short, the whole job of making cloth, from cutting the material to packing the finished product, is the maker's responsibility.
-
Progressive Bundles System
This production system is similar to the section production system, but all the machines are lined, and a different operator operates each machine. The cut parts of the garments are placed in a bundle form. The operator receives the bundle, performs their operation, and then moves the cut part to the following operators to perform different processes over the garment.
There are several operators performing sewing over the garment. One of the practical advantages of using this method is that operators are skilled and efficient, increasing work performance.
In this way, consistency is generated from product to product. A lot of exporting manufacturers adopt this method of clothing manufacturing.
In this way, consistency is generated from product to product. A lot of exporting manufacturers adopt this method of clothing manufacturing.
-
One-piece Flow System
Unlike the progressive bundle system, a bundle contains all the product's components in one piece flow system. The sewing machines are placed in a straight line. The only difference in this method is that the operator works over the piece and then passes the garments to the following operators so that everyone can perform a different operation in a flowing system. This flow system is less time taking.
-
Modular Production System
In this type of production system, all the operators work together as a team to create the garment. In this type of manufacturing, some multi-skilled operators form a group, and these operators do multiple operations.
The whole team helps the different to manufacture the finished garment quickly. In this manufacturing, the entire team working on the garment is responsible for the quality and production of the garment.
The team performance is counted and measured in this production system, while the other type measures individual performance.
-
Overhead Production System (OPS)
In this manufacturing system, the clothes or the pieces of the clothes are hung over the hanger, and the hanger is placed over the overhead rail. This hanger contains the components of a single piece. We can also say this is one of the single-piece flow systems.
Two Main Methods of Garment Production
Clothing manufacturers commonly use two primary methods.
1. CMT (Cut, Make, and Trim)
2. FPP (Full Production Package)
Here are both of these methods defined:
CMT (Cut, Make, and Trim)
In the CMT method, the services included are cutting, making, and trimming that turns the raw materials into the finished product.
To use this manufacturing method, you need to have skills in these processes.
- Cutting
- Trimming
- Sewing
The method starts with the cutting of the fabric right according to the requirements of the technical packs and patterns. After cutting, the fabric is sewed together. The sizes and shapes of the material are set and adjusted according to the grading sheet provided. After manufacturing the fabric, several quality checks are performed to test the fabric's quality and durability. It is checked if the material meets the customer requirements.
Advantages of CMT
- Control over fabric selection
- Extra packaging
- Swing tags
- A suitable method for demanding retailers
- Latest technology and machinery
- Specification sheets
- Cost-effective
Complete Production Package (FPP)
In FPP, the clothing garments are undergone all the stages of the product development. Here are some different stages of the garment manufacturing.
- Fabric and trims
- Sample development
- Pattern making
- Production of Final garment
As the name tells, FPP includes both CMT along with all the other factors in the manufacturing of the garments.
In this type of manufacturing, the manufacturers consult with the brand, and after collecting the requirements, the initial sketches are used to create the technical packs. This is a vastly distributed method, which helps in fabric sourcing and selection. In this way, the final garment is manufactured.
Advantages of FPP
- Uses of the whole process of product development
- Tech pack development
- Wide fabric sourcing
- High on demand
- Ensures the consistent traffic
- Cutting, trimming, sewing
Wrapping up
The manufacturing process is a pretty lengthy process that includes a number of processes. The guide explains each step of the garment manufacturing process. There might be an addition in the number of steps based on the customers' requirements.